Seminar on Non Conventional Machining Report Download
抽象的
Non-traditional machining (NTM) processes are now being widely used to generate intricate and accurate shapes in materials, like titanium, stainless steel, high strength temperature resistant (HSTR) alloys, fiber-reinforced composites, ceramics, refractories and other difficult-to-machine alloys having higher strength, hardness, toughness and other diverse material properties. Generation of complex shapes in such materials by the traditional machining processes is experienced to be difficult. For effective utilization of the capabilities of different NTM processes, careful selection of the most suitable process for a given machining application is often required. Selection of the best suited NTM process for a work material and shape feature combination requires the consideration of several criteria. In this report, various NTM process have been explained which can be used by the user for different applications.
Examples of traditional machining processes are turning, boring, milling, shaping, broaching, slotting, grinding etc. Similarly, Abrasive Jet Machining (AJM), Ultrasonic Machining (USM), Water Jet and Abrasive Water Jet Machining (WJM and AWJM), Electro-discharge Machining (EDM) are some of the Non Traditional Machining (NTM) Processes.
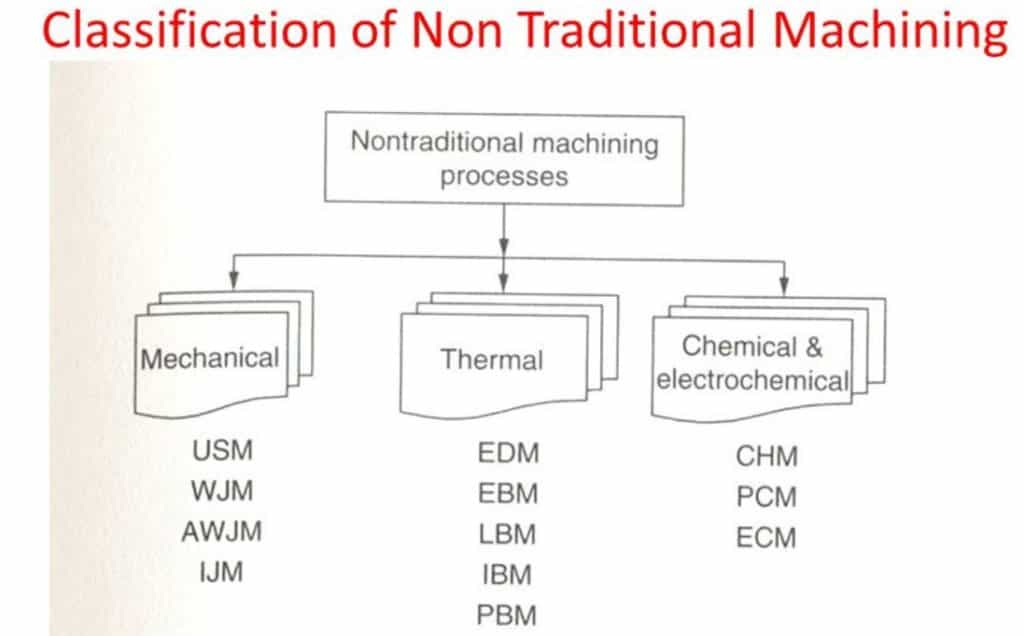
磨料喷射加工(AJM)
磨料喷射加工(AJM), also known as micro-abrasive blasting, is a mechanical energy based unconventional machining process used to remove unwanted material from a given workpiece.
The process makes use of an abrasive jet with high velocity, to remove material and provide smooth surface finish to hard metallic workpieces. It is similar to Water Jet Machining (WJM).
Ultrasonic Machining (USM)
USM是机械材料去除过程或用于通过使用成型工具,高频机械运动和磨料浆料侵蚀硬质或脆性工件上的孔或空腔的研磨工艺。USM提供了扩大加工脆性需求的解决方案
materials such as single crystals, glasses and polycrystalline ceramics, and increasing complex operations to provide intricate shapes and workpiece profiles. It is therefore used extensively in machining hard and brittle materials that are difficult to machine by traditional manufacturing processes. The hard particles in slurry are accelerated toward the surface of the workpiece by a tool oscillating at a frequency up to 100 KHz – through repeated abrasions, the tool machines a cavity of a cross section identical to its own. A schematic representation of USM is shown in Figure .
水射流切割
Water jet cutting can reduce the costs and speed up the processes by eliminating or reducing expensive secondary machining process. Since no heat is applied on the materials, cut edges are clean with minimal burr. Problems such as cracked edge defects, crystalisation, hardening, reduced wealdability and machinability are reduced in this process.
Chemical Machining (CM)
Chemical machining (CM) is the controlled dissolution of workpiece material (etching) by means of a strong chemical reagent (etchant). In CM material is removed from selected areas of workpiece by immersing it in a chemical reagents or etchants; such as acids and alkaline solutions. Material is removed by microscopic electrochemical cell action, as occurs in corrosion or chemical dissolution of a metal. This controlled chemical dissolution will simultaneously etch all exposed surfaces even though the penetration rates of the material removal may be only 0.0025–0.1 mm/min. The basic process takes many forms: chemical milling of pockets, contours, overall metal removal, chemical blanking for etching through thin sheets; photochemical machining (pcm) for etching by using of photosensitive resists in microelectronics; chemical or electrochemical polishing where weak chemical reagents are used (sometimes with remote electric assist) for polishing or deburring and chemical jet machining where a single chemically active jet is used. A schematic of chemical machining process is shown in Figure .
Electrochemical Machining (ECM)
Electrochemical machining (ECM) is a metal-removal process based on the principle of reverse electroplating. In this process, particles travel from the anodic material (workpiece) toward the cathodic material (machining tool). A current of electrolyte fluid carries away the deplated material before it has a chance to reach the machining tool. The cavity produced is the female mating image of the tool shape.
Electrical Discharge Machining (EDM)
Electrical discharge machining (EDM) is one of the most widely used non-traditional machining processes. The main attraction of EDM over traditional machining processes such as metal cutting using different tools and grinding is that this technique utilises thermoelectric process to erode undesired materials from the work piece by a series of discrete electrical sparks between the work piece and the electrode. A picture of EDM machine in operation is shown in Figure
Laser–Beam Machining (LBM)
激光束加工是热材料去除过程,其利用高能,相干光束来熔化和蒸发在金属和非金属工件的表面上的颗粒。激光可用于切割,钻孔,焊接和标记。LBM特别适用于准确放置孔。激光束加工的示意图示于了图中。
Electron Beam Machining (EBM) – Modern Machining Process
Electron Beam Machining (EBM) is a thermal process. Here a steam of high speed electrons impinges on the work surface so that the kinetic energy of electrons is transferred to work producing intense heating. Depending upon the intensity of heating the work piece can melt and vaporize. The process of heating by electron beam is used for annealing, welding or metal removal. During EBM process very high velocities can be obtained by using enough voltage of 1,50,000 V can produce velocity of 228,478 km/sec and it is focused on 10 – 200 μM diameter. Power density can go up to 6500 billion W/sq.mm. Such a power density can vaporize any substance immediately. The Complex contours can be easily machined by maneuvering the electron beam using magnetic deflection coils. To avoid a collision of the accelerating electrons
with the air molecules, the process has to be conducted in vacuum. So EBM is not suitable for large work pieces. The process is accomplished with vacuum so no possibility of contamination. There are no effects on work piece because about 25-50μm away from machining spot remains at room temperature and so no effects of high temperature on work.
CONCLUSION
非传统的加工方法具有与传统的加工方法相比具有若干具体优势。它使任务看起来更容易。这些方法不受材料的硬度,韧性和脆性的限制,并且可以通过合适地控制过程的各种物理参数在任何工件材料上产生任何复杂的形状。这些方法在生产治疗中找到了生产的若干产品,具有更好的质量和精确值和最低成本。
Despite the traditional methods as recent advancements non-traditional methods are adequate to machine, any type of materials from stand point of economic production. The word untraditional is used in the sense that the metal slide hastalloy, nitraalloy, mnemonics are such that they can’t be machined by traditional methods but require some special techniques where the untraditional methods stand firmly. So now a day’s even having traditional methods as advancement several industries prefer the non-traditional methods.
Download