Table of Contents
What is Inspection
- Inspection is the most common method of attaining standardization, uniformity, and quality of workmanship. It is the cost art of controlling the product quality after comparison with the established standards and specifications.
- It is the function of quality control. If the said item does not fall within the zone of acceptability it will be rejected and the corrective measures will be applied to see that the items in future conform to specified standards.
- An inspection is an indispensable tool of the modern manufacturing process. It helps to control quality, reduces manufacturing costs, eliminates scrap losses, and assignable causes of defective work.
Inspection Definition :
“ inspection is part of quality”- inspection is the checking, verification of raw material, in-process, semi-finished or finished components. It is the first step to distinguish between accepted or rejected components.
Inspection basically involves;
1. Interpretation of specifications/ drawings.
2. Measurement of dimensions or other related parameters.
3. Selection of proper instruments, gauges.
4. Selection of units of measurements.
5. Comparison between specified and measured values.
6. Based on the act of comparison proper decisions to be taken.
Inspection is the first and basic act to towards achieving the quality defined from customer’s requirements, hence inspection is part of quality.
Objectives of Inspection
1. To collect information regarding the performance of the product with established standards for the use of engineering production, purchasing, and quality control, etc.
2. To sort out the poor quality of manufactured products and thus to maintain standards.
3. To establish and increase their reputation by protecting customers from receiving poor quality products.
4. Detect the source of weakness and failure in the finished products and thus check the work of the designer.
Need of Inspection in Industry:-
Needs of the inspection in manufacturing:-
1) To ensure that the part, material, or component confirms the established standard.
2) To meet the interchangeability of the manufacturer.
3) To maintain customer relationships by ensuring that no faulty product reaches the customer.
4) Provide the means of finding out shortcomings in manufacture.
5) It helps to purchase a good quality of raw material, tools, equipment which governs the quality of the finished product.
6) It helps to coordinate the functions of quality control, production, purchasing, and other departments of the organization.
7) To take decisions on the defective parts.
Purpose of Inspection
1. To distinguish good lots from bad lots
2. To distinguish good pieces from bad pieces.
3. To determine if the process is changing.
4. To determine if the process is approaching the specification limits.
5. To rate the quality of the product.
6. To rate the accuracy of inspectors.
7. To measure the precision of the measuring instrument.
8. To secure products – design information.
9. To measure process capability.
Stages of Inspection
1. Inspection of incoming materials:
It is also called receiving inspection. It consists of inspecting and checking of all the purchased raw materials and parts that are supplied before they are taken on to the stock or used in actual manufacturing. The inspection may take place either at the supplier’s end or at the manufacturer’s gate. If the incoming materials are large in quantity and involve huge transportation cost it is economical to inspect them at the place of vendor or supplier.
2. Inspection of the production process:
The work of inspection is done while the production process is simultaneously going on. Inspection is done at various work centers of men and machines and at the critical production points. This had the advantage of preventing wastage of time and money on defective units and preventing delays in assembly.
3. Inspection of finished goods:
This is the last stage when finished goods are inspected and carried out before marketing to see that poor quality products may be either rejected or sold at reduced prices.
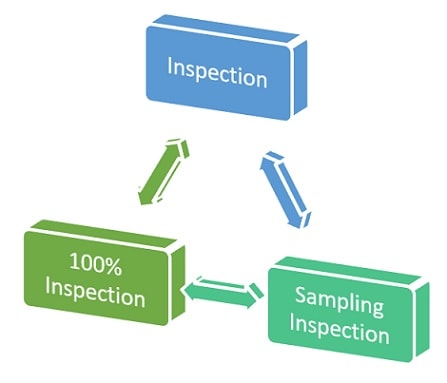
Methods of Inspection: Types Of Inspection
There are two methods of inspection.
1. 100% Inspection:
- This type will involve careful inspection in detail of quality at each strategic point or stage of manufacture where the test involved is non-destructive and every piece is separately inspected. It requires more inspectors and hence it is a costly method.
- 没有抽样误差。这是接受我nspection error arising out of fatigue, negligence, the difficulty of supervision, etc. Hence complete accuracy of influence is seldom attained.
- It is suitable only when a small number of pieces are there or a very high degree of quality is required.
- Example of 100 % inspection:Jet engines, Aircraft, Medical, and Scientific equipment.
100 % Inspection is not preferred in the industry for mass production due to the following reasons.
- The cost required for inspection is more as compared to sampling inspection.
- The time required for inspection is more
- The operator suffers from inspection fatigue.
- More staff is required for inspection.
- Due to more handling chances of damage increase.
- 100 % inspection not possible where destructive testing is required.
2. Sampling Inspection:
- 在这个方法中随机选择样本inspected. Samples taken from different batches of products are representatives. If the sample proves defective. The entire concern is to be rejected or recovered.
- Sampling inspection is cheaper and quicker. It requires less number of Inspectors. It’s subjected to sampling errors but the magnitude of sampling error can be estimated.
- In the case of destructive tests, random or sampling inspection is desirable.
- This type of inspection governs wide currency due to the introduction of automatic machines or equipment’s which are less susceptible to chance variable and hence require less inspection, suitable for inspection of products which have less precision importance and are less costly.
- Example:Electrical bulbs, radio bulbs, washing machines, etc.
- Destructive tests conducted for the products whose endurance or ultimate strength properties are required.
- Example:Flexible strength, resistance capacity, compressibility, etc.
Types of sampling plans:-
1. Single sampling plan.
2. Double sampling plan.
3. Multisampling plan.
Double sampling plan:-In double sampling plan the decision on acceptance or rejection of the lot is based on two samples
Example:-
Parameters, N= lot size = 500
n1= number of pieces in the first sample. =35
C1= acceptance number for the first sample. =1
n2= number of pieces in the second sample. =50
C1= acceptance number for the second sample. =4
1. Take the first sample of 35 items from a lot of 500 and inspect.
2. Accept the lot on the basis of the first sample, if it contains 0 or 1 defective.
3. Reject the lot on the basis of the first sample if it contains more than 4 defectives.
4. Take a second sample of 50 items if the first sample contains 2,3 0r 4 defectives.
5. Accept the lot on the basis of the first and second sample combined, if the combined sample of 85 items contains 4 or fewer defectives.
6. Reject the lot on the basis of the combined sample if the combined sample contains more than 4 defectives.
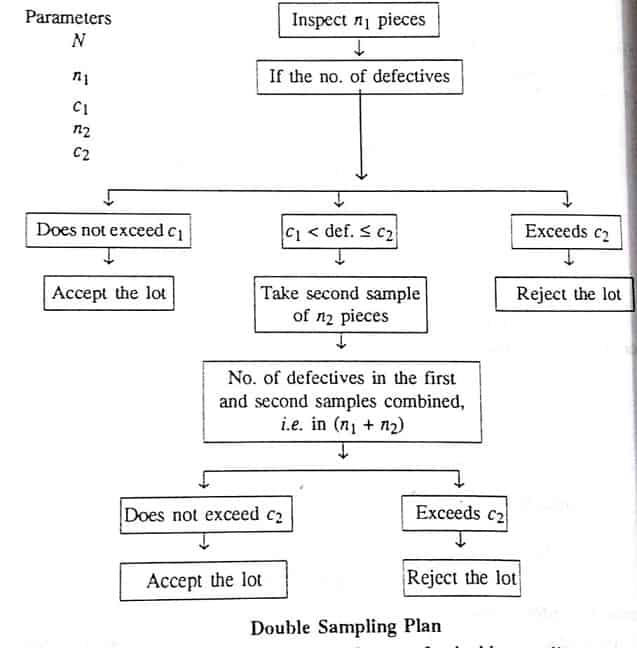
Advantages of Sampling Inspection:
Sampling inspection is more practical. a quick and economical method of taking decision regarding acceptance or rejection of the purchased or manufactured items. The advantages of sampling inspection are :
- The items which are subjected to destructive test must be inspected by sampling inspection only.
- The cost and item required for sampling inspection is quite less as compared to 100 % inspection.
- The problem of inspection of fatigue which occurs in 100 % inspection is eliminated.
- Less inspection staff is necessary.
- Less damage to products because only few items are handled during the inspection.
- The problem of monotony and inspector error introduced by 100 % inspection is minimized.
- The lot is disposed off in shorter period so that scheduling and delivery dates are improved.
- The most important advantage of sampling inspection is that it exerts more effective pressure on quality improvement. Since the entire lot may be rejected only on the basis of the sample.
Disadvantages of Sampling :
Some of the disadvantages of Sampling Inspection are:
- 在抽样检验,因为只有部分是inspected the sample may not represent the exact picture obtaining in the lot, hence there is likely hood or risk of making wrong decisions about the lot.
- The costs of rejected lots will be passed on by the producer on the consumer.
- This method may not be suitable for taking decisions on acceptance or rejection of a very costly and important item.
- It is necessary to use random sampling, select proper sample size, and acceptance numbers for accurate results.
Disadvantages of Inspection
- Inspection adds to the cost of the product but not for its value.
- It is partially subjective, often the inspector has to judge whether a product passes or not.Example:Inspector discovering a slight burnish on a surface must decide whether it is bad enough to justify rejection even with micrometers a tight or loose fit change measurement by saying 0.0006 inches. The inspector’s design is important as he enforces quality standards.
- Fatigue and Monotony may affect any inspection judgment.
- Inspection merely separates good and bad items. It is no way to prevent the production of bad items.
Difference between Sampling acceptance / Sampling Inspection and 100 % Inspection :
Compare acceptance sampling with 100% inspection
1) Thecost requiredfor sampling inspection is quite less as compared to 100% inspection.
2) Thetime requiredfor sampling inspection is less as compared to 100% inspection.
3) In sampling inspection problem ofinspection fatiguewhich occurs in 100% inspection is eliminated.
4) Smallerinspection staffis necessary for sampling inspection as compared to 100% inspection.
5) In sampling inspectionless damage to the product, because only a few items are subjected to handling during the inspection.
6) The problem ofmonotony and inspector errorintroduced by 100% inspection is minimized.
7) Sampling inspection exerts more effective pressure on quality improvement. Since the rejection of the entire lot on the basis of sampling brings much stronger pressure on quality improvement than the rejection of individual articles.
8) Sampling inspection providesless informationabout the product than 100% inspection.
9) Some extraplanning and documentationrequired in sampling inspection.
Difference between Inspection and Quality Control
Inspection | Quality control |
---|---|
Inspection is a part of quality | Concerned with confirmation with specifications |
Act of checking the components | An effective system of integration of various functions |
Needs measuring instruments | Involves quality improvement tools |
Measurement activity | Analysis of measurement data |
More Resources /articles
Quality Control- Articles , notes , Interview Q and A
Measurement Science and Metrology Notes , Articles